Daar is 'n verskeidenheid van vervaardigingsprosesse om 'npasgemaakte metaaldeel. Elkeen het sy eie stel voordele en nadele. Sommige van die belangrike faktore wat die keuse van 'n proses beïnvloed, sluit die volgende in:
- Hoeveelheid van die materiaal benodig
- Ontwerp van die metaaldeel
- Vereiste toleransies
- Metaal spesifikasie
- Oppervlakafwerking benodig
- Gereedskapskoste
- Ekonomie van bewerking versus proseskoste
- Afleweringsvereistes
Casting
Die gietproses bestaan uit die giet of spuit van gesmelte metaal in 'n vorm wat 'n holte bevat met die gewenste vorm van diegietstukke. Metaalgietprosesse kan geklassifiseer word volgens die tipe vorm of deur die druk wat gebruik word om die vorm met vloeibare metaal te vul. As die gietproses volgens die tipe vorm geklassifiseer kan word in sandgietwerk, beleggingsgietwerk en metaalgietwerk; terwyl deur die druk wat gebruik word om die vorm te vul, die gietproses verdeel kan word in swaartekraggiet, laedrukgiet en hoëdrukgiet.
Grondbeginsels van gietwerk
Gietery is 'n stollingsproses. Daarom kan die mikrostruktuur fyn ingestel word, soos korrelstruktuur, fasetransformasies en neerslag. Defekte soos krimpporositeit, krake en segregasie is egter ook intiem gekoppel aan stolling. Hierdie defekte kan lei tot laer meganiese eienskappe. ’n Daaropvolgende hittebehandeling word dikwels benodig om oorblywende spanning te verminder en meganiese eienskappe te optimaliseer.
Voordele van gietwerk:
- Groot en komplekse metaalgietprodukte is maklik.
- Hoë produksietempo, veral deur outomatiese gietlyn.
- Ontwerp buigsaamheid is beskikbaar en meer geskik.
- Diverse metaal beskikbaar: grys yster, rekbare yster, koolstofstaal, legeringstaal,vlekvrye staal, aluminiumlegering, koper, brons en sinklegering.
Nadele van gietwerk:
- Defekte binne die gietstukke
- Krimp porositeit
- Metaalprojeksies
- Krake, warm skeur, koue sluite
- Rondtes, oksiede
- Misloop, onvoldoende volume
- Insluitings
- Vereis noukeurige prosesbeheer en inspeksies (porositeit kan voorkom)
Smee
Smee is 'n vervaardigingsproses waar metaal deur plastiese vervorming onder groot druk tot hoësterkte dele gevorm word. Afhangend van of die smeevorm gebruik word, word die smeeproses ingedeel in oop smee en smee. Maar as deur die temperatuur van die gesmede metaal en legering voor smee, kan die smeeproses verdeel word in koue smee, warm smee en warm smee.
Grondbeginsels van smee
Smee of koue vorming is metaalvormingsprosesse. Daar is geen smelting en gevolglike stolling betrokke nie. Plastiese vervorming veroorsaak 'n toename in die aantal ontwrigtings wat lei tot 'n hoër toestand van interne spanning. Trouens, rekverharding word toegeskryf aan die interaksie van ontwrigtings met ander ontwrigtings en ander hindernisse (soos graangrense). Terselfdertyd verander die vorm van primêre kristalle (dendriete) na plastiese bewerking van die metaal.
Voordele van smee:
- Goeie meganiese eienskappe (vloeisterkte, rekbaarheid, taaiheid)
- Betroubaarheid (gebruik vir kritieke onderdele)
- Geen vloeibare metaalbehandeling nie
Nadele van smee:
- Die ontvul
- Die mislukking
- Vorm beperk wanneer ondersny of kerngedeeltes vereis word
- Algehele koste gewoonlik hoër as gietwerk
- Veelvuldige stappe word dikwels vereis
Ons kan warm werk van koue werk onderskei. Warmbewerking word bo die herkristallisasietemperatuur uitgevoer; koudbewerking word daaronder uitgevoer. In warm werk word rekverharding en verwronge korrelstruktuur baie vinnig uitgeskakel deur die vorming van nuwe rekvrye korrels as gevolg van herkristallisasie. Vinnige diffusie by warm werkstemperature help om die voorvorm te homogeniseer. Aanvanklike porositeit kan ook aansienlik verminder word, uiteindelik heeltemal genees word. Metallurgiese verskynsels soos rekverharding en herkristallisasie is belangrik omdat hierdie veranderinge in struktuur 'n toename in rekbaarheid en taaiheid oor die giettoestand tot gevolg het.
'n Belangrike ding om in gedagte te hou, is dat kwaliteit van materiaal en hittebehandeling in sommige gevalle 'n belangriker faktor kan wees as die verskil tussen giet en smee.
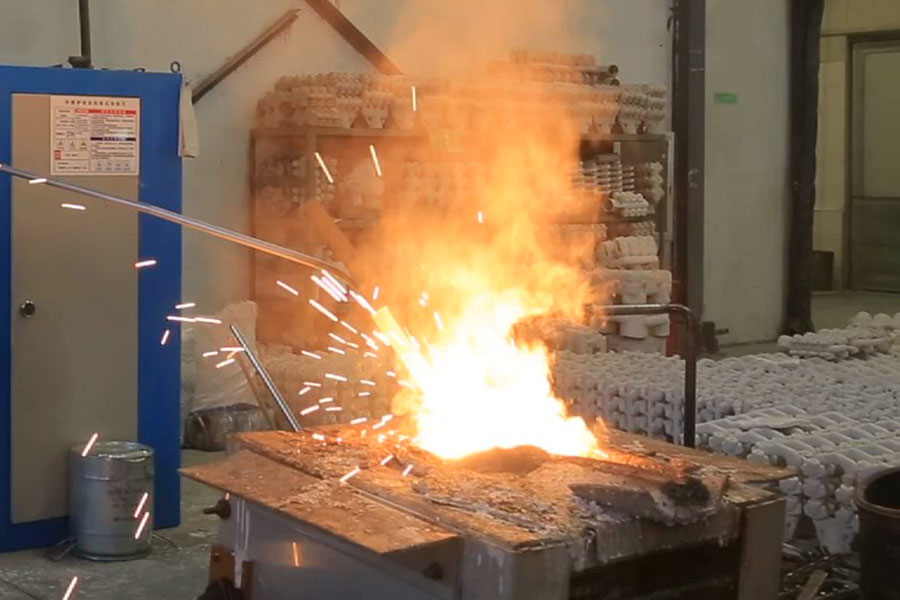
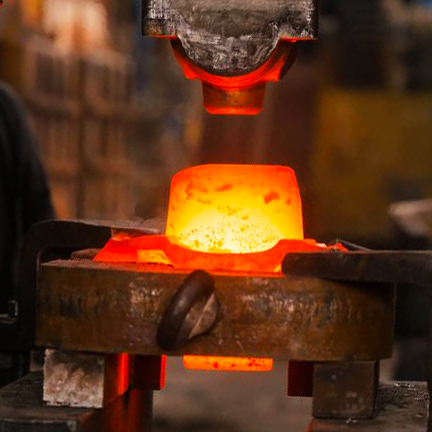
Postyd: 24 Februarie 2021